by Blair White
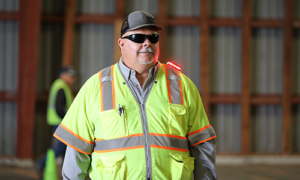
PCCA Safety & Compliance Coordinator Forrest Doshier
It has been a season of wins for the PCCA Warehouse Division. During its annual evaluation with insurance company Texas Mutual, the cooperative received zero recommendations for improvements to its safety efforts. The fast pace of a warehouse receiving and shipping cotton can be hazardous, so this excellent news proves employees’ hard work is paying off.
“Warehouse facilities are visited to better understand operations,” said Eddie Gonzales, Texas Mutual Senior Safety Services Consultant. “During visits, employees are observed performing their duties. Visual observations are made of operations being conducted in the recognition of potential injury-causing hazards. Policies and procedures are reviewed to ensure safety programs are designed to address the most prevalent hazards observed.”
There are many moving parts to keep improving, especially inside cotton warehouses. Texas Mutual was very satisfied with what they saw during their visit.
“Observations made of your warehouse operations revealed employees working in a safe manner throughout the facility,” Gonzales said. “Forklift operator training was always up to date, and employees were conducting operations safely. Engineering controls were put in place to reduce the likelihood of injury to employees. Facility safety features were in place to prevent mishaps with the loading and unloading of trailers. Employee empowerment was noted with a safety committee being in place to address safety concerns and to promote safe working practices throughout the organization.”
Sweat Equity
Despite the significant improvements in the Warehouse Division safety record, efforts are still being made each day to make the safety programs better than they have ever been. Forrest Doshier, PCCA’s Compliance and Safety Coordinator, and the Warehouse team, have voluntarily requested consultations from companies like Texas Mutual and OSHA. Many consultations are free and have proven to be a valuable resource for the cooperative.
“I like other people coming in and looking at our operations with a fresh set of eyes,” Doshier explained. “They see things I don’t, and that helps us get a better program.”
Doshier and his team also have introduced improved training, safety incentives, pilot programs, and more. It is no small feat to receive such positive feedback from a safety evaluation, but the work is never finished. It takes vigilance from all employees to make sure operations continue running safely.
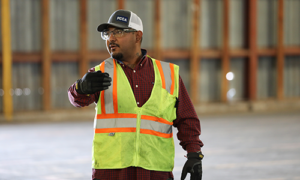
PCCA Sweetwater Warehouse Plant Manager Ralph Munoz
“Safety standards and regulations are always changing, and we have to stay current with those,” he said. “It takes a consistent approach to do that. Annual reviews are one of the requirements that should be done. We have written safety programs, the managers are doing training at the plants, and we are still trying to improve on their training skills by providing more education.”
Being proactive is as crucial as having reactive policies and procedures. Employee education and feedback are the best ways to prevent incidents.
“A lot of it comes from education,” Doshier said. “Sometimes employees don’t understand hazards in the workplace, and identifying those hazards is a big step in making it safe. We are listening to our employees’ concerns and we are taking action. We are coming in, doing training, and explaining why something may or may not be hazardous. Then they are seeing the changes being made to make their workplace safer.”
Every employee at PCCA’s warehouse facilities, whether in an administrative position or hands-on labor, undergoes training in safety fundamentals and tailored content for each job. Increased safety means less downtime from injuries, resulting in lower insurance premiums that save PCCA money and add value to grower-owners’ cotton.
Tomorrow’s Plans
PCCA is focused on being the cooperative of the future for its growers. Achieving that goal means managing risks in every part of the company. Tomorrow’s plans call for innovative thinking today.
“I have several goals,” Doshier said. “Number one is being able to continue the downward trend on our numbers. Number two, I’d like to see us establish two training centers where we bring new hires to complete their training with bilingual instructors. As you progress through your career, you could come back to the training center and display your skills and move up through different levels in the warehouse. I’d also like to see us create a leadership academy for people who would like to advance in the company.”
Doshier’s plans are not just conceptual. Some concrete actions he and his team have been making include creating pilot programs, enrolling in additional OSHA safety resources, and gaining continuity between warehouse plant operating procedures. Putting in sweat-equity to go the extra mile makes all the difference in making PCCA’s warehouse facilities a safe workplace.
“My other goal is to get us in the SHARP program (Safety and Health Achievement Recognition Program) through OSHA for small businesses,” he said. “If you are involved in that, they already know you are working toward the safety standards you need to be. That would get us an instance where we wouldn’t have to have a compliance officer come to the facility, just someone to do a consultation.”
Effective communication and continuity between plants is vital.
“Because we have so many different plants, one of the things we are working on is getting our standard operating procedures down in writing and consistent from plant to plant,” he said. “So, if we are bringing crews down from Kansas to Texas, we want everything to be consistent except for the few minor things that are naturally different because it’s a different plant.”
No matter the location, one thing remains true — every action is designed to add value to grower-owners’ cotton. Safety plays a vital role in keeping operations running smoothly and efficiently while providing additional opportunities to put more money back into farmers’ pockets.
Defining Safety
Courtesy of LADWA Solutions, Inc.
There are many moving parts in a cotton ware- house, and so much effort goes into making them as safe as possible for employees, but what does safety really mean?
Accidents – an unexpected event that results in serious injury or illness of an employee and may also result in property damage.
Near miss – a narrowly avoided accident.
Incident – An instance of something happening, an unexpected event or occurrence that does not result in severe injury or illness but may result in property damage.
All accidents are incidents, but not all incidents are accidents (which happen about 2% of the time). They have in common that both events are unplanned and can cause damage to places or things. So, an incident can involve a near miss, where someone narrowly avoided injury or illness, but it’s an accident if a severe injury occurs.
Ultimately, every incident that occurs provides the potential for a future near miss or accident. To reduce the number of incidents and accidents that take place, implement a health and safety program that:
Identifies hazards – by reviewing employees, tasks, tools, and the environment, it is possible to identify hazards and risks within a work- place.
Implements controls – by implementing controls, it is possible to minimize the occurrence of incidents and accidents.
Investigates incidents – the importance of incident reporting should not be underestimated. When an incident is correctly reported and investigated, it ensures the root cause is found and that additional measures can be implemented to avoid a reoccurrence.