Warehouse Receipts Exceed Early Estimates
By Jayci Cave
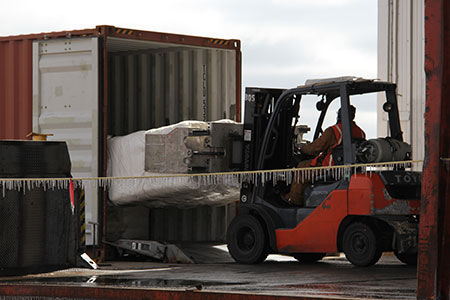
A warehouse employee loads a truck for shipment in the cold weather in Altus, Oklahoma.
Plains Cotton Cooperative Association’s Warehouse Division employees have risen to the challenge to handle this year’s crop which is significantly larger than originally expected. The early estimates predicted the division would receive approximately 950,000 bales, and the estimate is now 1,150,000. When handling a crop of this magnitude, the Warehouse Division has had many challenges to overcome to ensure everything runs smoothly and efficiently.
Tracy Springs, Warehousing North Regional Manager who manages the plants in Altus, Okla. and Liberal, Kan., said that storing a crop this large in the same amount of space and keeping up with the speed the cotton was coming in from the gins have been the primary challenges this year.
“If anyone had known that this crop was going to turn out as good as it has,” Springs said, “we would have started stacking the bales in the warehouses different from the start.”
In the Texas Rolling Plains area, Danny Helms, Warehousing South Regional Manager who oversees operations in Sweetwater, Rule and Big Spring, Texas, is expecting to receive approximately 100,000 bales more than the original estimate. He said this has caused more time to be spent handling the cotton and changed the way the cotton is stacked in the buildings.
Jay Cowart, PCCA’s Vice President of Warehousing, said they began stacking the plant in Sweetwater row stacked, two high with the early estimates and later realized they would have to switch to row stacked, three high.
“We stacked half of that plant or better two high before we discovered the crop had gotten larger,” Cowart said. “So then we converted to three high and now we are going to go back and restack those buildings to make enough space.” Helms said it can be difficult to find time and employees to restack the buildings.
“Once all buildings have been filled the first time and after shipping enough cotton to justify restacking a building,” Helms said, “you have to figure out how to come up with the time and employees to restack buildings and fill them up again with new cotton.”
In Altus, Springs said they are drastically exceeding the early estimate by 148,000 bales. With this increase, they have started to block stack all inbound cotton into 100 bale blocks instead of row stacking the cotton.
The difference between row stacking and block stacking is the process of locating the bale when it is time for it to be shipped. Row stacking is efficient because machine operators are able to get to any bale without having to move another bale. On the other hand, block stacking increases the labor and equipment requirements coming in and going out because in order to get to the bale employees need, they may have to move up to 50 bales of the 100 bale stack.
“This has enabled us to store 2,300 more bales per shed than we would normally be able to with conventional row stacking,” Springs said. “This gains us the equivalent of a shed for every three sheds that we fill. We also had to receive cotton in multiple locations to allow us to get the gin trucks unloaded in a timely manner due to the speed in which the cotton was being delivered.”
Cowart said they were two-thirds of the way through stacking the plant in Altus when they realized how large this crop was going to be. As a result, they will have to restack 20 of the 52 buildings in Altus to be able to fit this large crop.
“We have to do that after the end of the day,” Cowart said. “What happens is, there are current shipping orders that you are pulling out of this cotton that you need to restack. So, you can’t restack and not have it located because someone is going to come looking for that bale. Therefore, after the end of the day, a crew stays and works overtime to set those buildings back and get them relocated before time to start the next day.” Springs said it can also be challenging when you are pulling cotton from both row stacked and block stacked bales.
“Another challenge has been handling shipping orders that come out of both row stacked cotton and blocked cotton at the same time. The blocked cotton has to be broken out in rounds which requires us to have a sorting area so that the mix of multiple lots to be shipped can be placed together.”
Cowart said PCCA’s Information System’s Department helps with the process of pulling bales out of the block stacked cotton. They have written software that will show all of the cotton that is scheduled to come out of that block in the next few days. This allows them to get cotton for multiple orders when they break into a block of 100 bales. They also use color-coded bale tags when possible to make the bales easier for the warehouse employees to find.
The warehouse division has a total of 83 employees, 67 full-time and 16 seasonal, at all warehouse locations. Springs said they have had to hire additional employees to be able to handle the crop this year.
“All of these employees are new to the cotton warehouse world so there has been a great deal of training that had to be done,” Springs said, “however, they have done a great job, and I am very pleased with how well they have handled the learning process.” Cowart said PCCA has limited experience with block stacking cotton, but so far the transition is going well.
“Across a plant that is row stacked three high, you hope each employee can average getting 40 bales an hour out of the building,” Cowart said. “With block stacking, we were told to expect to initially get only about 20 bales per hour, and we are beating that substantially today.”
While dealing with the changes in procedure, the Warehouse Division employees have maintained a normal shipping schedule at all locations.
“We have a shipping standard in the warehouse business, and it is 4.5 percent of your CCC licensed capacity that you must provide per week. So all warehouses schedule that much or a little more. All of our plants right now have at least 21 days of that in front of them.”
PCCA warehouses are exceeding the 4.5 percent shipping standard, and Cowart said they currently are shipping about 7.0 to 7.5 percent of the CCC licensed capacity per week.
Cowart said he is amazed by the amount of work they are getting done at the plants. He expects that they will run approximately 460,000 bales through the plant in Altus this year.
“The plant’s capacity by the previous standards was 345,000 bales,” Cowart said, “when row stacked three high. In 2007, we ran 443,000 through here, all row stacked. It shipped fast enough and the receiving pace was slow enough that we could do that. In 2007, we restacked every single building on that plant once and some twice. This time, that won’t occur because of the block stacking.”
Although it is hard to determine what the end results will be, Cowart said he is anticipating the income to rise a little more than expenses for this crop year.
“Our fixed expenses are going to get allocated over additional bales driving fixed costs per bale down, but on the same hand our variable costs of having to restack and block stack will go up,” Cowart said. “On a per bale basis, I think it will be close to a push, but I expect income to rise a little more than expenses.”
Helms said the employees have adapted well to all the changes they have faced this year, and they have helped the process go smoothly by working smarter and offering their ideas on how they could improve on procedures. Springs said having experienced employees also has made a difference this year, and he is proud of their hard work and dedication.
“We have a great group of employees, and I think they can adapt to any challenge that we throw at them,” Springs said. “This has been a whole new experience for them as well as myself, and they have taken it all in stride and are doing an excellent job. They take pride in what they are doing, and they want to be the best at it for themselves and for PCCA. They have had to work a lot of long, hard hours yet they show up to work everyday with no complaints. I would put the employees that we have up against anyone, and I know they will shine.”