By Sarah Hossain
Cotton Incorporated has, yet again, found a way to enhance a popular apparel item: denim. This time around, Cotton Incorporated has created Storm Denim, a new finish that repels water while providing an extra level of durability and tear resistance.
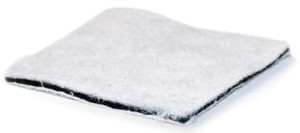
An example of a decontamination wipe.
“Our goal was to offer a high degree of water repellency for use in rainwear and outerwear while maintaining the comfort and breathability of cotton,” said Cotton Incorporated Director of Textile Chemistry Research William A. Rearick. “[We wanted] to offer something highly functional and useful to the consumer.”
The new finish has been featured in Textile World magazine and was named “The Best Cure for Market Saturation” by DNR, a menswear trade publication. In addition to functionality, the new finish also makes denim more fashionable.
“In the jeans segment, it’s always about the next new thing,” said Mark Kametches, Cotton Incorporated Account Executive. “The industry has seen water- repellant denim finishes before, but usually applied in fabric form,” he explained. “Applying in garment-form means that almost any denim finish can accept the technology; creating more consumer benefits, more marketability for specific end uses and with that, more sales.”
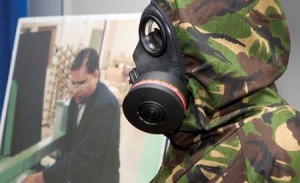
Dr. Seshadri Ramkumar hopes to make emergency gear more comfortable while offering protection against hazardous material.
Cotton Incorporated is not the only organization creating new uses for cotton. In 2000, Dr. Seshadri Ramkumar of Texas Tech University’s Institute of Environmental and Human Health began research to develop several uses of cotton. In 2005, he found a use for cotton in the form of protective wipes and liners for the U.S. military. The development consists of nonwoven cotton fabrics containing activated charcoal for protection against chemical warfare. He said the Department of Defense was interested in creating a new decontamination wipe.
Ramkumar’s research was funded by several sponsors including the U.S. Department of Defense, Texas Food and Fiber Research Program, The CH Foundation in Lubbock, Cotton Foundation of the National Cotton Council and Plains Cotton Growers, Inc.
Dr. Ramkumar and his team tested several fabrics, and the best performing wipe came from Texas Tech University. His goal was to create a decontamination wipe that was non particulate, meaning non-powder form.
Not only will our military personnel be better protected from chemical weapons, emergency workers also will have increased protection. When responding to spills, workers usually wear heavy, uncomfortable uniforms. Dr. Ramkumar is attempting to change the gear emergency workers wear so they do not have to be uncomfortable for long periods of time. By sandwiching specific cleaners such as activated carbon between layers of nonwoven cotton cloth, Ramkumar will be designing a fabric that can be used to make comfortable clothing liners while offering protection against hazardous materials. Dr. Ramkumar uses nonwoven material because of its practicality.
“Woven is expensive because it involves spinning yarn,” he said. “With the nonwoven fabric you can make it cheaper. It can be used once and then thrown away. Cotton is used in bleached form in the fiber stage before making nonwovens to make it absorbent.”
Ramkumar says the technology he has created also can be used for chemical cleanup wipes, air filters and other products used for adsorption where protection is necessary.
“If you add other functional chemicals to the wipes it would have biological protection. The use of bleached cotton results in a high-end, value-added cotton product for the entire industry.” He also said bleached cotton will absorb chemical toxins without dissolving.